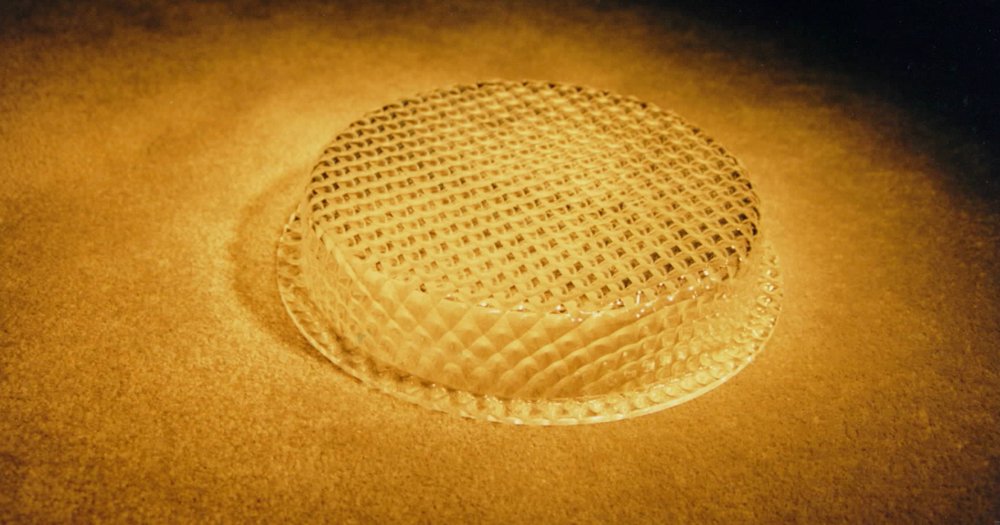
Pressure Forming
Plastic Pressure Forming
The Process:
Plastic sheet is heated in an oven
Heated plastic sheet is presented to the mold
Mold is thrusted into heated plastic sheet and the vacuum is turned on
Pressure is then turned on (upwards of 100psi) on the backside of the heated plastic sheet to completely press against the mold; adhering to additional detail not achieved in typical vacuum forming (details such as logos, mold texture, and sharp corners)
After the part is formed and cool down process is completed, the part is removed
Now the part is ready for all necessary secondary operations (trimming, drilling, finishing, etc.)
Plastic Pressure Forming
Advantages:
Uniform material gauge throughout deep molds for even part distribution
Highly cosmetic parts are achieved
Achieve sharp and crisp formed features
Short lead times
Less residual part stress
Tight tolerances with part repeat ability in high production runs
Multiple part textures can be achieved with textures and smooth areas on the same mold.
“We don’t have competitors, only companions in this industry, that’s why we supply them. That’s why even if your work is sourced from a different vendor, there’s a high probability that we produced it.”

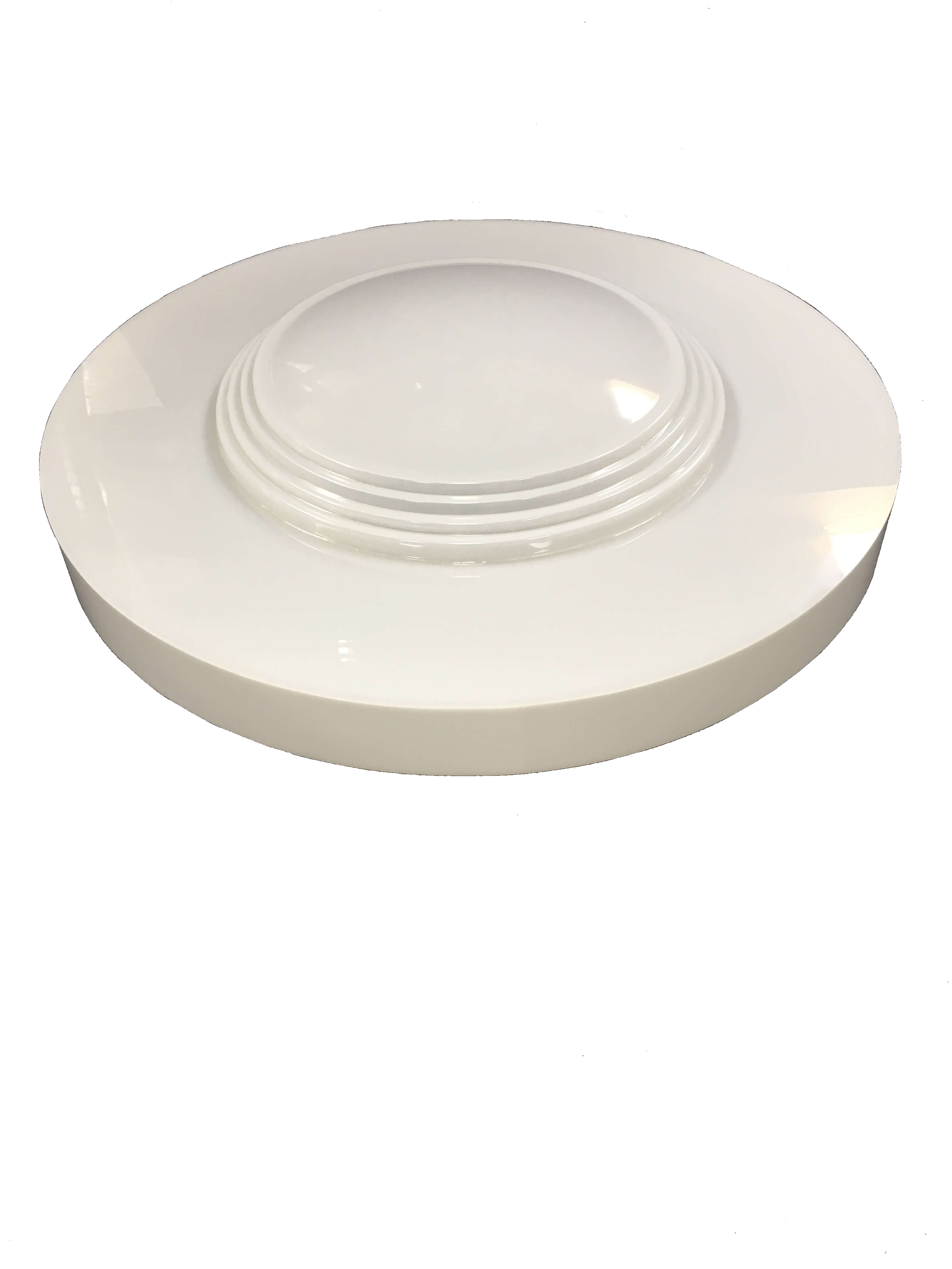
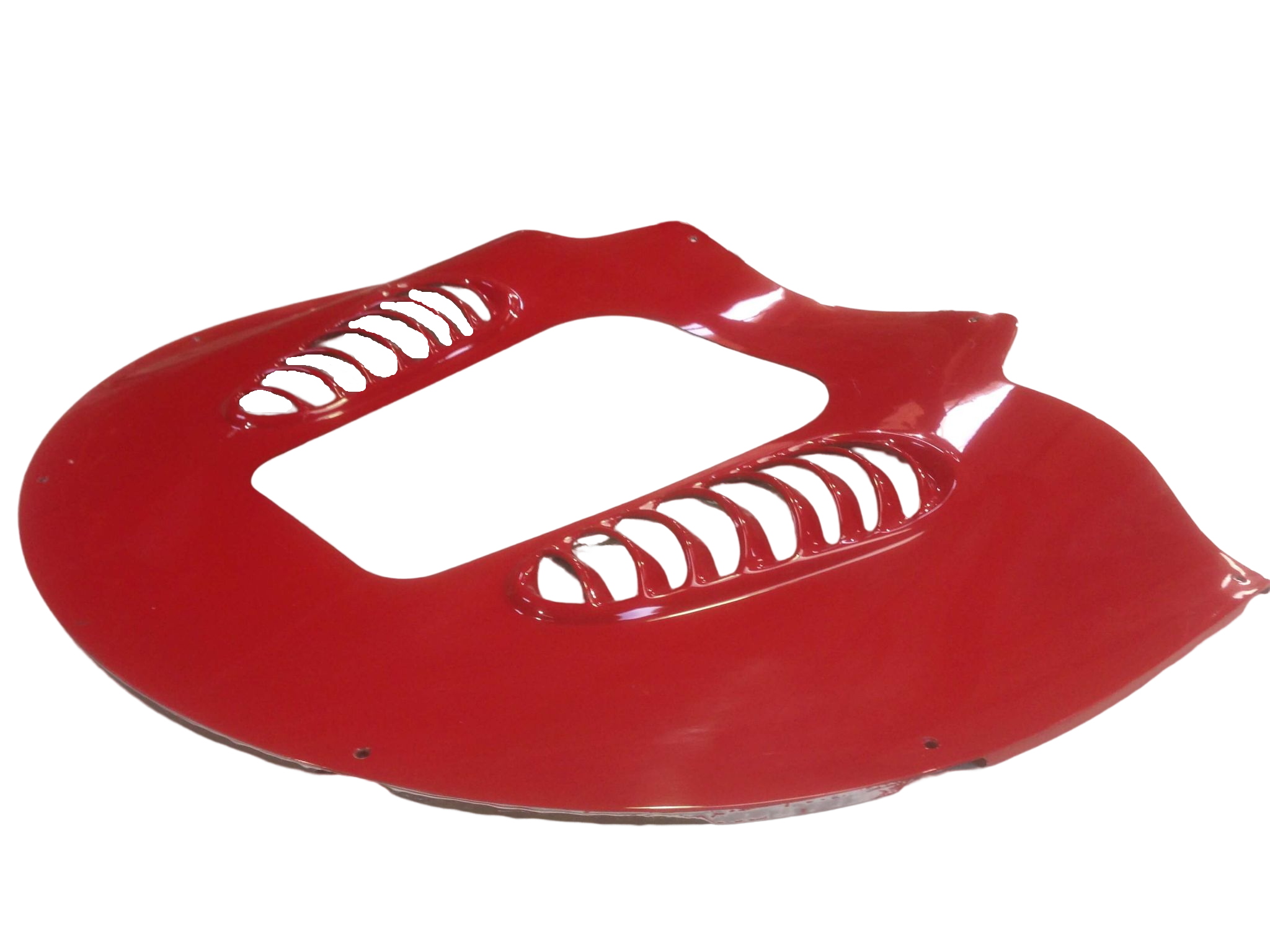

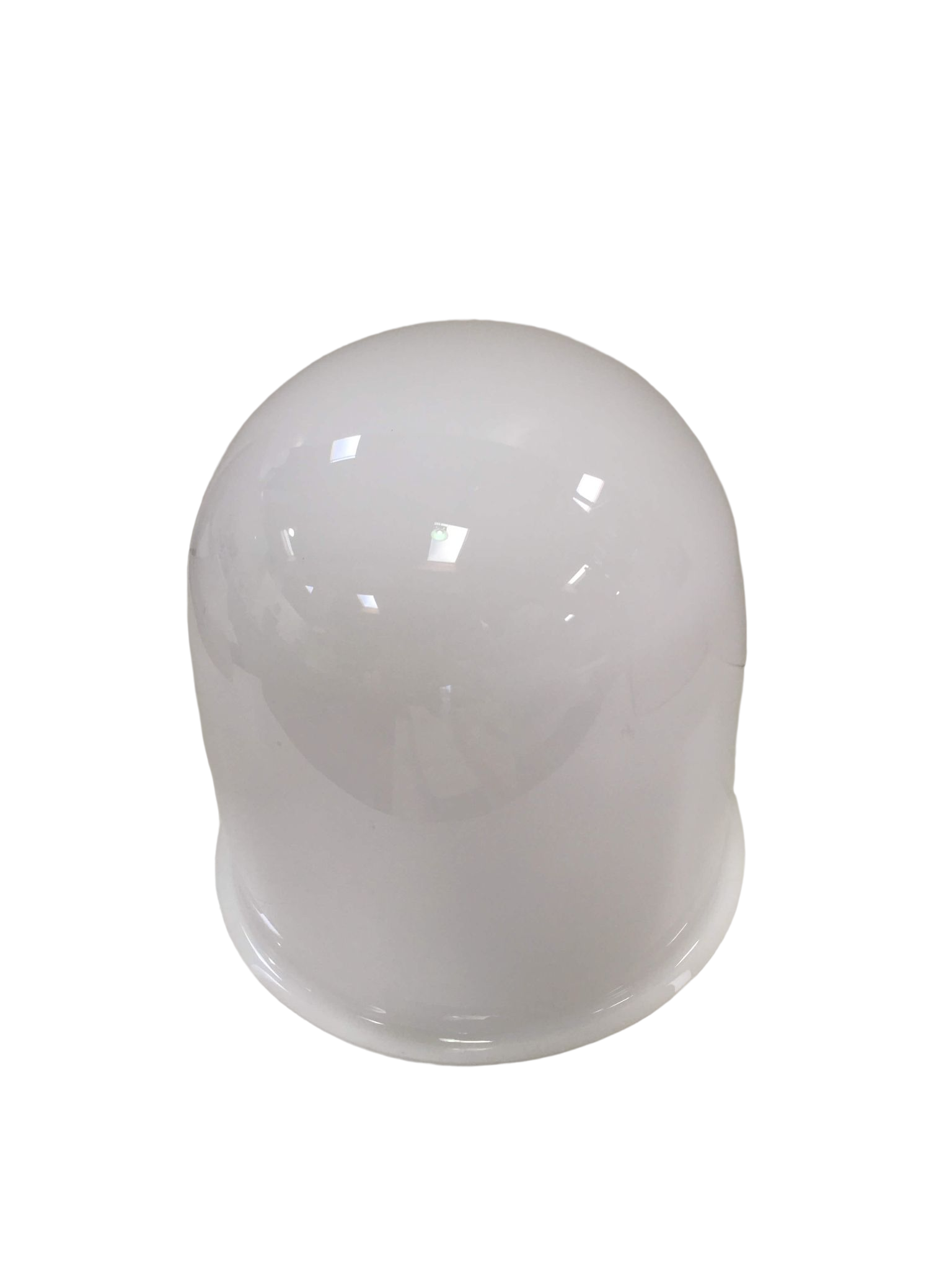

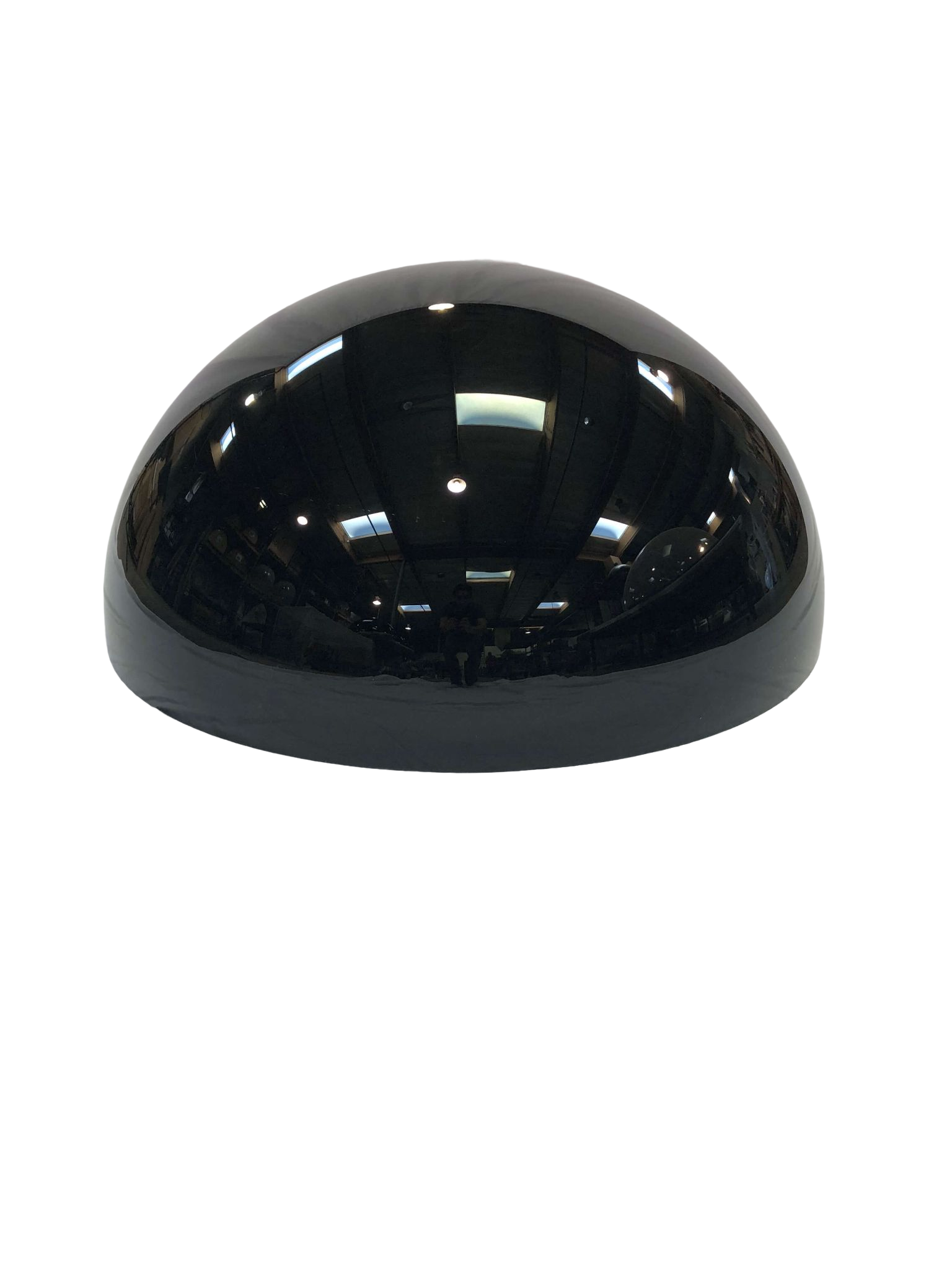
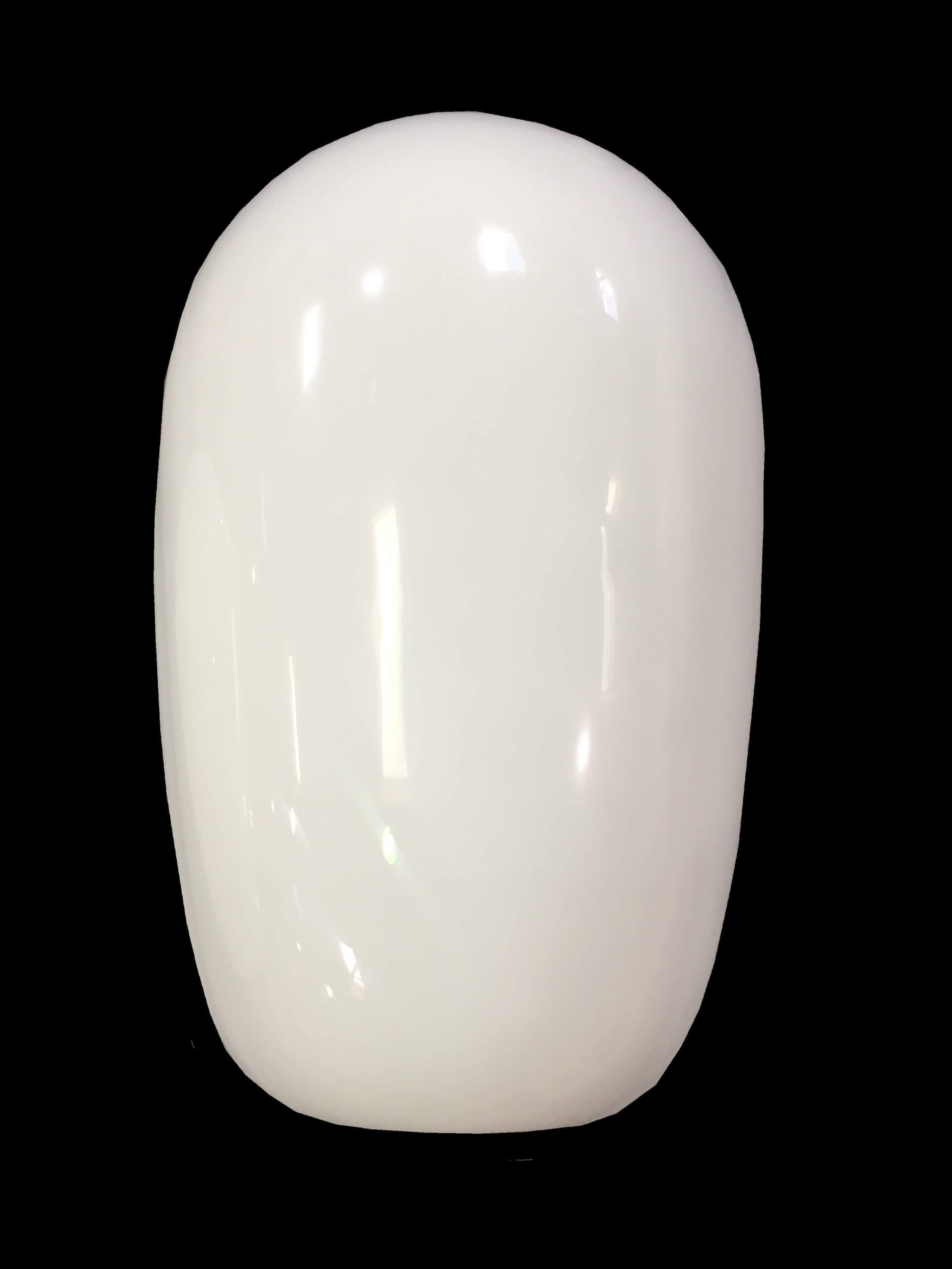
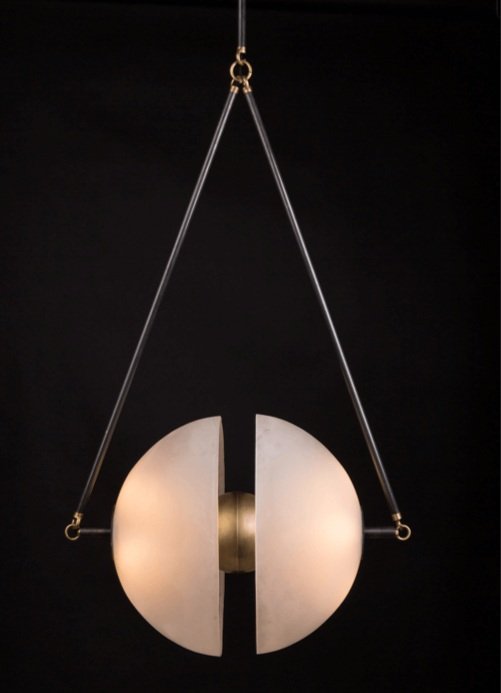
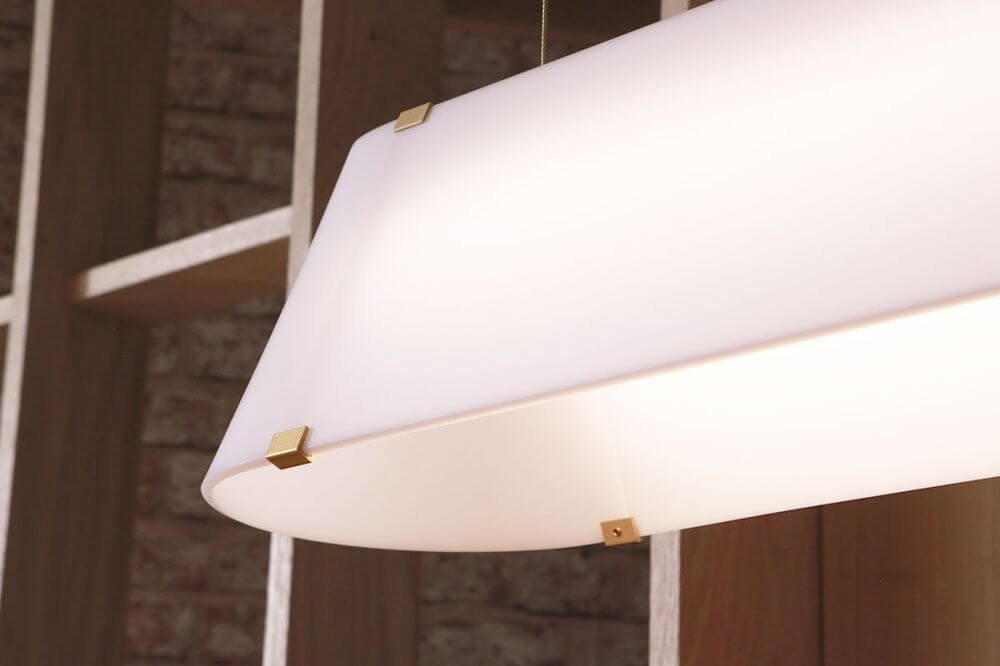
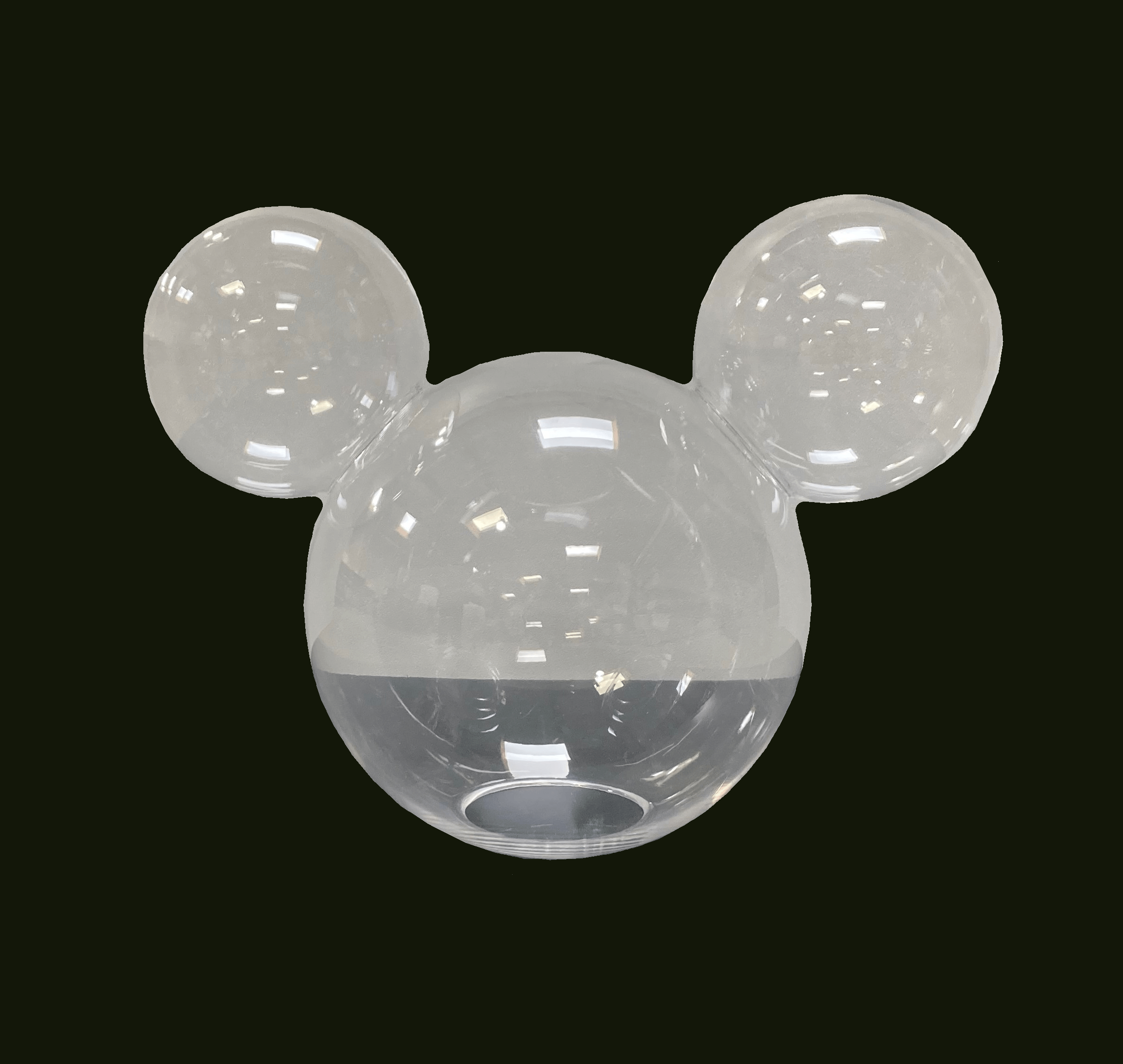

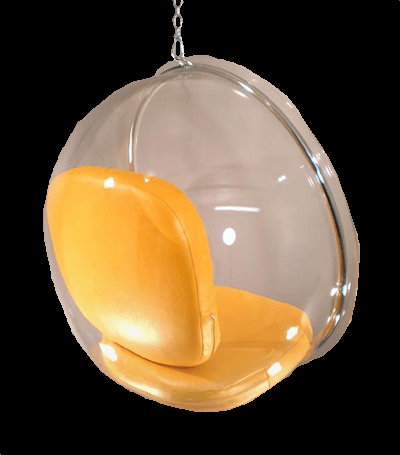
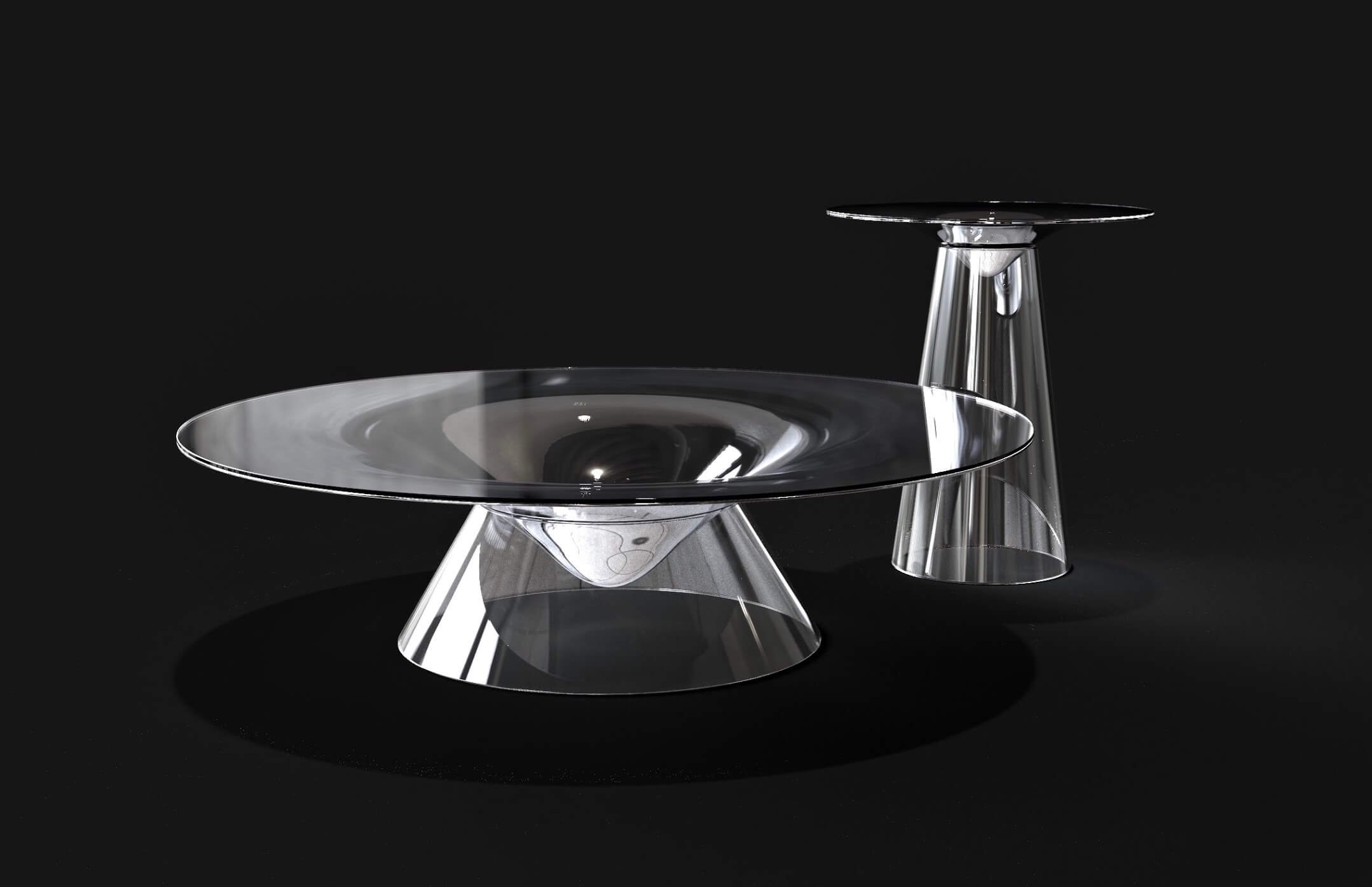
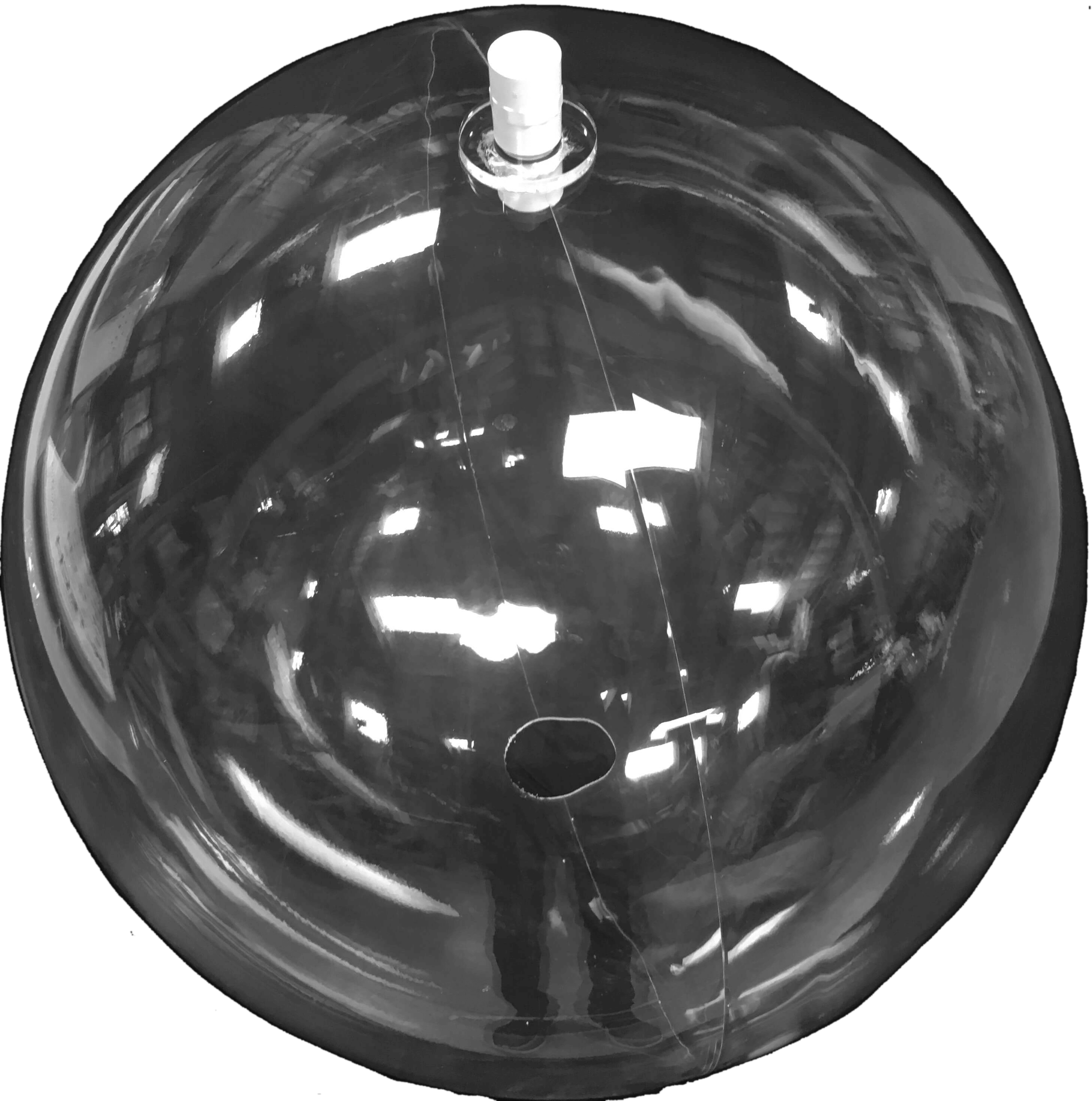